What We Can Learn From A Negative Review
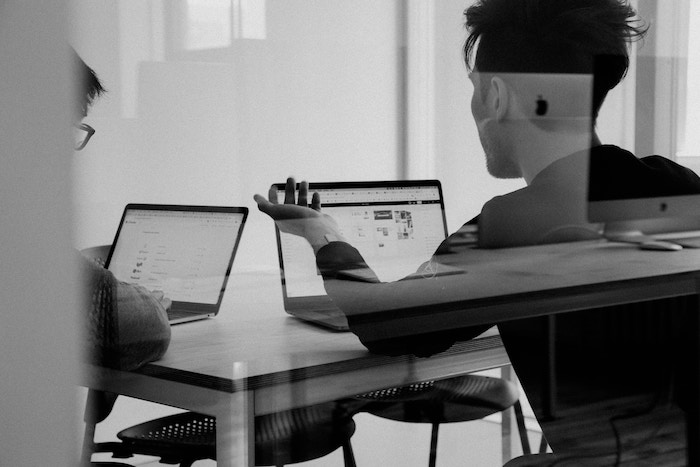
It is an unfortunate side of the business in this day and age that reviews can be written about a business by anyone and can cause a new enquiry like yourself concern about a business. We don’t get many of these reviews and it has taken me a long time to find the most positive way to reply to these comments. I have decided to use each experience as an example of the many ways development and production can go wrong in this deceptively difficult industry. I hope that you learn something from this review reply to help in your own journey. If you have any further questions about this example then I am more than happy to discuss with you. Just give me a call.
The below blog is in reply to a message posted by Lia L, a past Mentee who wrote 2/5 stars.
Julia and the Sample Room team are lovely. The samples I received, however, were not.
Julia puts in a great deal of time and effort into the Mentorship Program and does all that she can to equip emerging designers with as much information as possible in launching their own business. Her patience, continuous support and experience are truly inspiring and commendable. For that, I would rate the Fashion Label Launchpad mentorship course 4/5 stars.
If you’re looking to get your designs made up into garments, however, my advice is to simply find a professional patternmaking company who focus specifically in this area (as opposed to spreading themselves over training courses, their own label etc etc.)
Due to the poor fit and finishing of the garments I received (and had paid a great deal for), I unfortunately had to have these re-made again by another company. So, having had samples made from both Sample Room and then another Patternmaking company, I found the quality and fit of the garments made by the patternmaking professionals to be of a much higher standard, along with a pricing structure that was ultimately cheaper and had a lot more clarity. I would rate this aspect of the business 1/5 stars.
If your designs are quite simple, then your experience may be different. Good Luck!
My reply was posted below.
Hello Lia,
Thank you for your kind words on the Fashion Label Launchpad Mentoring program. We take great pride in the hard work that we have put in to help educate those starting out in the industry to understand the steps that need to be taken, along with the possible pitfalls. It saddens me that you have had a negative experience during the development process despite the information given in the program on the steps that need to be taken to ensure success.
For some people reading this review, it might be helpful to understand the process and what possibly went wrong in this instance with your garments to help them avoid this situation themselves in the future.
First of all, the relationship between a designer and pattern maker is complex one. The quality of information given has a direct relationship to the quality of the product delivered at each stage, which is why working with start-ups can sometimes be complex. Understanding of design elements, construction and language needed to communicate this with the service providers such as a patternmaker is often lacking. At the end of the day, a pattern maker is part interpreter and part mind reader. A good pattern maker is always up for the challenge but there are no pattern makers anywhere in the world who can take a complex garment and get it 100% right in the first sample. We often start with a toile to get the basic fit, length and design lines correct in the quickest, cheapest way before progressing to the sample fabric to then see how the fabric reacts. There is then a fitting to fine tune before another sample is made before production. Please read below how this process was interrupted and stopped half way through, resulting in a disappointing result.
2-The designs were very complex styles. They were based on sketches with no reference images or examples of the special features you requested to get a true understanding of what you had in mind or if it in fact could be done. These special features included cut outs, strapping, pleated bust cups, low V front and back in the tops, unusual ways of attaching bodices and skirts on the waist, cross over waistbands that were unclear as to whether they were sewn down or separate and separate sleeves to be attached in difficult, untested ways that were going to take trial an error to achieve. In addition to this the added complexity of difficult fabrics such as stretchy fake leather, chiffon and sueded fabric sewn together created tricky garments that would require more work than a basic t-shirt or dress. We had discussed in the initial meeting that these garments were tricky and the fabric was very hard to work with. I thought that you understood that this might take a toile and 2 samples when you said ‘that’s OK I like it’.
3-After a design meeting, we completed a pattern, toile and a toile fitting where many of the make details were discussed. There are many and varied ways a garments can be made and finished and often the language needed to communicate what is in a designers head is lacking at the start of their career, so it is harder to get the right information. We then proceeded to make the sample up in the sample fabric provided. This is a very important step as we start to see how the pattern reacts in the fabric and see how we need to adjust the pattern to make the design work. We don’t topstitch the garment (or in the case of a flat locked garment, we would only overlock) as we are always mindful of time and cost so we create the garment without these final details until the fit and design is correct. We would normally proceed to a Sample fitting in-house on the stand the pattern was created for. We would discuss the fit and finish of the garment, pin out the garment and trouble shoot any changes that need to be made. Unfortunately for you Lia, against our wishes, we changed this step to assist you in looking at the garments in your own time as you had been so happy with the process so far. The garments were collected after we were satisfied with an internal fitting on the mannequin.
We then received an unhappy email from you with photos of the garments taken on another stand but not zipped up and a photo of a garment on a smaller body shape but unfortunately you were not willing to come in and fit these garments despite offers to stay back after work and assist in any way that we could. You were unwilling to proceed with the normal process of developing a garments so we resolved to send you the patterns as DXF files.
It does not surprise me that the new pattern maker was able to achieve such a great result. As they then picked up the job, imported the patterns, used the garments to solve the fit problems and completed the development process with patterns already created and a sample to see how to improve the pattern. In reality they got the easy part of the job after the discussion, interpretation and finalisation of the job, creating a beautiful sample as we would have at this stage. For those reading, the process of development always follows the following steps.
Design meeting-Pattern-Toile-Fitting-Alteration-Sample-/-Fitting-Alteration-Sample-Fitting-Alteration-Grading-Markers-Production. This path allows for 2 samples. Simple styles sometimes only need a toile and sample and some styles have been known to go through the sample process 5 times (this does not happen often in our business but ask anyone who works for larger labels and they will often be in this situation. In this case the other pattern maker at Sample Room who spent 6 yrs at Bardo, 6 yrs at Portmans and various other business said it would take her 5 samples to get designs like yours correct). As you can see I have put a -/- where we were forced to stop the process with Lia. As you can imagine this left us as frustrated as Lia. If only we could have proceeded to the next stage. Even though I have worked for 24yrs in the fashion industry and complete 1000’s of different garments from sportswear to swimwear, wedding dresses and fashion, we sometimes unfortunately do not reach the expectations of some designers despite making every effort to give them the knowledge needed. This happens very rarely, maybe 1 in every 5000 designs and there is always a breakdown in the process that has resulted in this. I have written this long post to help the reader and I hope they have learnt something about the process, what is involved and how it can go downhill without the knowledge needed. Please check out our blog on our website (www.sampleroom.com.au) for more topics and to see what others have said about their own journey. I am passionate about education in the fashion industry if only because no-one should be accused of poor workmanship when the customer did not follow the usual procedures or misunderstand the importance of the steps put in place to ensure the right result.
So often we are asked by new designers to the industry, what do I need to know? Or why do I need to do a course to get my designs made, can’t you just do it? Hopefully the above explanation of what can go wrong and the information that a designer needs to bring to the design meeting will give you just a hint of the knowledge that is required. More importantly this is a great example of why we unfortunately can only work with start-ups who are open to training in our Mentoring program as without this knowledge and support, the difficult journey of development and manufacturing can result in an unhappy relationship, which is the last thing we would ever want. Thank you Lia for showing a perfect example of why an understanding of the process is critical to all parties feeling happy with the result. I wish you luck in the future with your label.